What Does Alcast Company Mean?
What Does Alcast Company Mean?
Blog Article
A Biased View of Alcast Company
Table of ContentsMore About Alcast CompanySome Known Details About Alcast Company The Best Guide To Alcast CompanyFascination About Alcast CompanyAlcast Company - TruthsThe Ultimate Guide To Alcast Company
Chemical Comparison of Cast Light weight aluminum Alloys Silicon advertises castability by decreasing the alloy's melting temperature and boosting fluidity throughout casting. Additionally, silicon adds to the alloy's strength and wear resistance, making it beneficial in applications where resilience is critical, such as automotive components and engine parts.It also enhances the machinability of the alloy, making it easier to refine into finished products. In this way, iron contributes to the overall workability of aluminum alloys.
Manganese contributes to the strength of aluminum alloys and boosts workability. Magnesium is a light-weight element that gives strength and effect resistance to aluminum alloys.
Indicators on Alcast Company You Should Know
Zinc improves the castability of aluminum alloys and assists manage the solidification process during spreading. It enhances the alloy's strength and firmness.
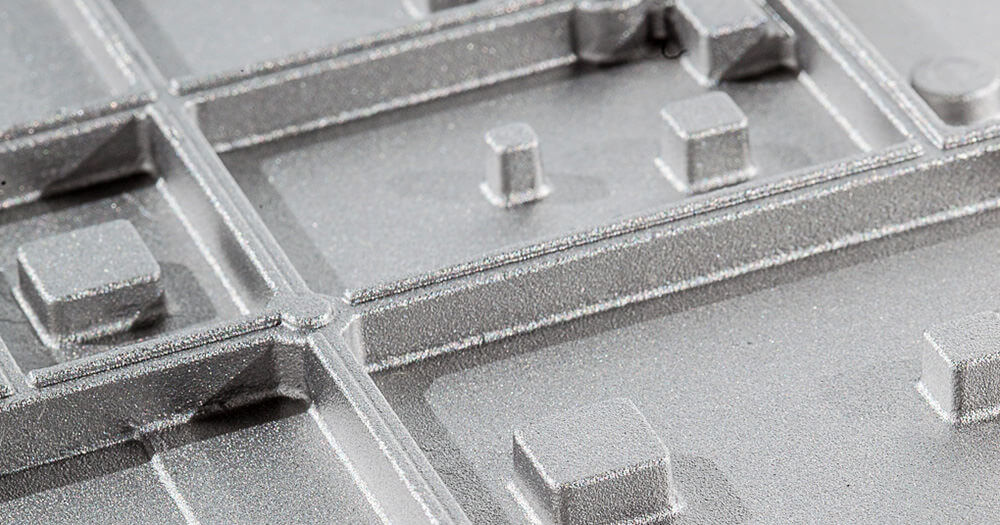
The primary thermal conductivity, tensile stamina, yield strength, and prolongation vary. Select suitable resources according to the efficiency of the target item created. Among the above alloys, A356 has the highest possible thermal conductivity, and A380 and ADC12 have the cheapest. The tensile limitation is the opposite. A360 has the ideal return stamina and the highest possible prolongation price.
The Ultimate Guide To Alcast Company

In precision casting, 6063 is fit for applications where detailed geometries and high-grade surface area coatings are extremely important. Examples include telecommunication enclosures, where the alloy's exceptional formability enables for streamlined and visually pleasing styles while maintaining structural integrity. In the Illumination Solutions industry, precision-cast 6063 elements create elegant and effective lights fixtures that need detailed shapes and excellent thermal efficiency.
It brings about a finer surface area coating and much better rust resistance in A360. The A360 exhibits remarkable prolongation, making it ideal for facility and thin-walled elements. In precision spreading applications, A360 is fit for industries such as Customer Electronic Devices, Telecommunication, and Power Tools. Its boosted fluidness enables intricate, high-precision components like smart device cases and interaction tool housings.
Some Of Alcast Company
Its unique homes make A360 a beneficial option for accuracy spreading in these sectors, improving product longevity and high quality. aluminum casting manufacturer. Aluminum alloy 380, or A380, is a commonly made use of spreading alloy with several distinctive qualities.
In precision casting, light weight aluminum 413 beams in the Customer Electronics and Power Tools sectors. This alloy's remarkable rust resistance makes it a superb selection for outside applications, ensuring long-lasting, long lasting items in the discussed sectors.
Fascination About Alcast Company
The aluminum alloy you pick will considerably affect both the spreading process and the properties of the last product. Due to the fact that of this, you need to make your choice thoroughly and take an informed technique.
Establishing the most ideal aluminum alloy for your application will certainly indicate considering a wide array of attributes. These comparative alloy attributes follow the North American Pass Away Spreading Association's standards, and we have actually divided them right into two categories. The first category addresses alloy features that affect the production procedure. The 2nd covers attributes affecting the residential or commercial properties of the end product.
Getting The Alcast Company To Work
The alloy you select for die casting directly impacts several aspects of the spreading procedure, like how easy the alloy is to collaborate with and if it is susceptible to casting issues. Warm cracking, additionally referred to as solidification cracking, is a regular die casting problem for light weight aluminum alloys that can result in internal or surface-level tears or splits.
Particular light weight aluminum alloys are extra prone to hot splitting than others, and your choice needs to consider this. It can harm both the actors and the die, so you must look for alloys with high anti-soldering properties.
Rust resistance, which is currently a notable quality of light weight aluminum, can vary considerably from alloy to alloy and is an important particular to take into consideration depending upon the environmental conditions your item will certainly be revealed to (Aluminum Casting). Use resistance is another building typically sought in click here for info light weight aluminum items and can separate some alloys
Report this page